ThinGap offers a wide range of modified-standard, full custom, and application-specific motor designs as a compliment to more than 50 standard products, as part of the TG and LS Series of motor kits. In addition, we have the ability to design and manufacture framed or housed motor assemblies as a pre-integrated solution. Finally, options like position sensors, carbon fiber components and enhanced process steps are available for programs with demanding requirements.
Modified and custom motor designs address the need for very specific performance specifications, operational requirements, cost optimized solutions and unique form factors that may be required for a project. Housed and framed assemblies enable more cost-effective, turnkey solution desired by projects with tight schedules which need to be able to rapidly integrate a motor into a system.
ThinGap regularly provides customers with custom motors or where possible, modified variants of its standard products. Additional information about each type of motor or generator design is provide below.
Custom and Optional Features
- Space rating
- Application specific designs
- Hall-effect position sensors
- Carbon fiber components
- Fiber wrapping for magnet retention
- Weight and cost optimized designs
- Environmental enhancements
- Redundant stator windings
- Direct-drive assemblies with encoder
- Optimized generator designs
- Extreme high powers (100kW+)
- Water resistant, submergible kits
- Requirements for M&P lists, onsite source inspection, and burn-in testing
Ground-Up Motor Design
(Typically 24-36 week lead time)
A fully custom product involves the ThinGap technical team working closely with the customer to design a motor kit which meets the exact specifications of an application, while also providing program and integration support by its team of knowledgeable engineers throughout the process. ThinGap has over 20 years of motor design experience, with proprietary design tools and precise analytical modeling, which allows for highly accurate as to performance, and rapid creation and build of custom motor designs. Custom designs offer the most flexible approach in meeting performance specifications, mechanical features, and cost objectives.
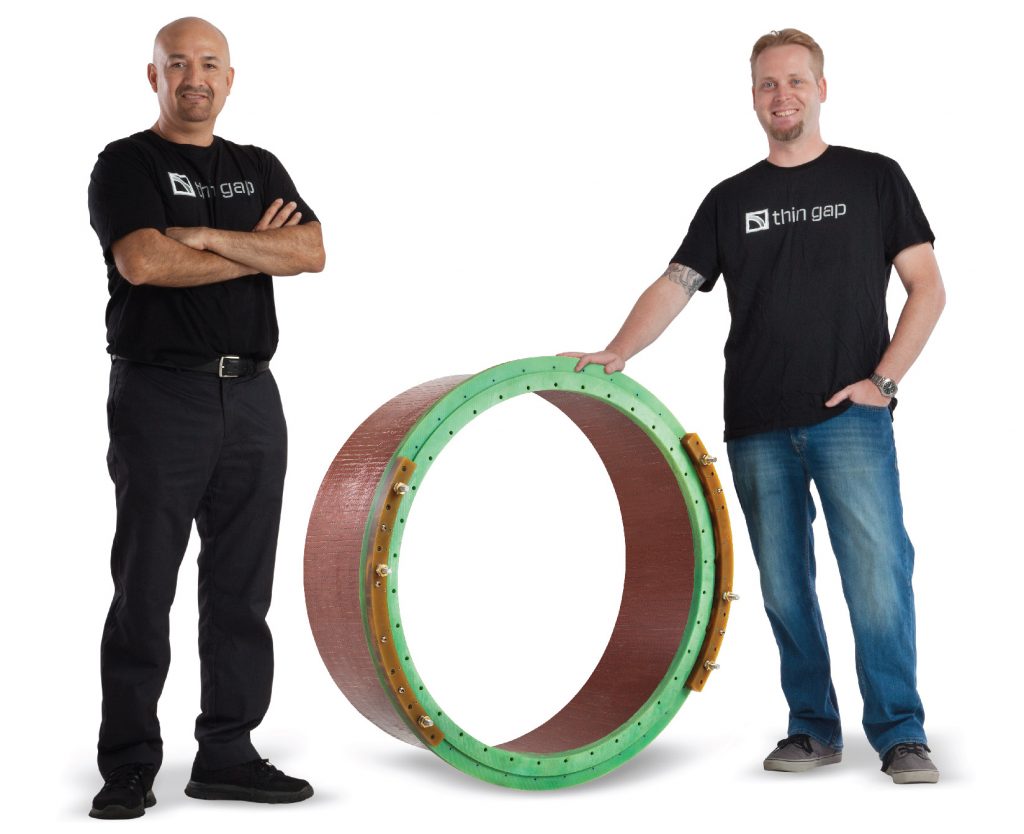
Custom High Power Applications
Minor Modifications
(Typically 8-10 week lead time)
Examples of smaller or minor modifications, which typically do not affect the lead time of off-the-shelf designs, include changes to the build process without impacting long-lead materials or modifications to tooling. This level of change carries a small NRE charge, in addition to a modest increase to the individual unit cost. Examples of minor modifications to standard product include:
- Alternate windings: enables a different distribution for the required input voltage and current without changing the output of the motor.
- Fiber Wrapped Rotors: rotor magnets can be wrapped in composite fiber for added retention, to allow the motor kit to reach higher speeds than the standard rating.
- High Temperature Materials: specific changes in base materials or adhesives used in the motor to allow for more thermally extreme environmental operation.
- Water Resistant Coating: adding a water-resistant coating to the motor kit which allows for use in submerged applications, not limited to underwater propulsion and actuation.
- Additional Quality Requirements: beyond ThinGap’s standard comprehensive processes and testing of all products, additional quality and source inspection requirements can be supported.
Modified Ribbon Cable Assembly
Major Modifications
(Typically 14-18 week lead time)
More significant changes to an existing product usually require the ordering of long-lead materials and sometimes the fabrication of new tooling. Moderate NRE charges and a greater price increase per unit are typical with a major modified design.
- Vacuum Compatibility: replaces materials which do not conform to standard outgassing requirements, and adds leaded solder interconnects required in vacuum environments. Modification includes a material and processes (M&P) list, specialty PCB and solder implementation, in addition to outgassing data for all material used.
- Custom Housing: ThinGap will design and manufacture a custom framed or housed motor kit (either direct drive or geared) to customer specifications. Motor assemblies often include a bearing set, encoder for position control, unique housing design, and ThinGap can even source and integrate control or drive electronics as part of a turnkey solution.
- Carbon Fiber Components: Carbon fiber components used in the motor to optimize around overall system weight while maintaining the output of the kit.