As a leading maker of high-performance motor kits used in a range of applications, ThinGap’s staff recently completed its annual IPC J-STD Training and Certification.
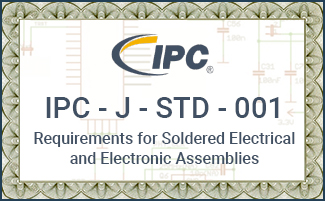
ThinGap is ISO 9001:2015 certified and supports customer-specific flow downs as part of program compliance and its Quality Management System. Industry-leading process and workmanship standards, such as IPC J-STD for soldering, are used throughout the production process. The annual training and certification of the J-STD is a key aspect of ThinGap’s quality control.
IPC is the global association that helps manufacturers and electronics industry suppliers build electronics and electronic components to higher standards. Like in years’ past, ThinGap production staff as well as quality control personnel underwent training to the IPC J-STD-001 specification. J-STD-001, is the Requirements for Soldered Electrical and Electronic Assemblies and the preeminent standard for electronics assembly manufacturing. The standard describes materials, methods, and verification criteria for producing a broad range of high-quality interconnections and emphasizes process control.
Workmanship standards, such as IPC J-STD and others like the American National Standards Institute or “ANSI” standards, are used throughout ThinGap’s production process. Furthermore, all documents and procedures are controlled by the Company’s Product Lifecycle Management (PLM) system.
ThinGap has a track record of supporting the exacting requirements for its base of Fortune 500 companies, Government customers including NASA, and regulatory specifications across multiple sectors, be it Space, Medical, Defense or Airborne.