As a recent example of its custom motor capabilities, ThinGap recently shipped an assembly in support of a defense project that utilizes structural carbon fiber composite components to increase performance. While the company is no stranger to working with composites, with many current off-the-shelf products utilizing them, this project marks the first time these components have been sourced from a commercial vendor.
What is commonly referred to as “carbon fiber” in reality Carbon Fiber Reinforced Polymer (CFRP), a composite material typically composed of an epoxy-impregnated sheet of woven carbon-filament cloth that is layered, formed into a mold, and then cured in a kiln under vacuum conditions. The components made of the material that results from this process are extremely lightweight, and incredibly stiff with an excellent strength-to-weight ratio.
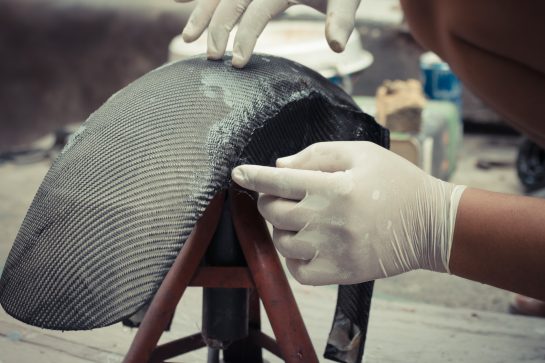
The individual fibers in modern carbon fiber are mostly composed of petroleum byproducts, with the development of pure, crystalline carbon fibers being how the material matured and was later industrialized. First synthesized throughout the late 19th and early 20th centuries, including by Thomas Edison for use as light filaments, these early attempts were unsuccessful as they were of low purity. It wasn’t until the early 1960s when Japanese and American chemists were able to produce fibers of the appropriate purity to be used as reinforcement in composites.
After substantial investment by the Royal Aircraft Establishment, a part of the British Ministry of Defense, the first industrially-produced carbon composite components came with the integration of a carbon composite compressor fan assembly in the Rolls-Royce Conway and RB-211 jet engines in the late 1960s. Through the 1970s, the material further matured with improvements in the quality of the filaments and adhesives, and by the early 1980s motorsports became another testbed for carbon composite materials.
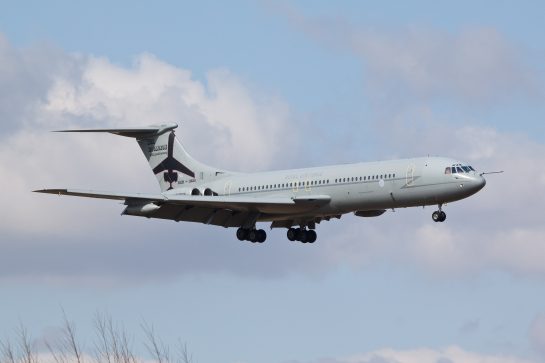
The Rolls Royce Conway jet engine was designed for the Vickers VC-10 Airliner
Introduced for the 1981 Formula 1 championship, the McLaren MP4/1 was an early racing car with a fully carbon composite chassis. Similar to the high-performance nature of aerospace, motorsports benefitted from composites by enabling weight reduction without sacrificing strength and rigidity, ensuring McLaren a competitive edge, and before long carbon composites were prevalent in all forms of racing.
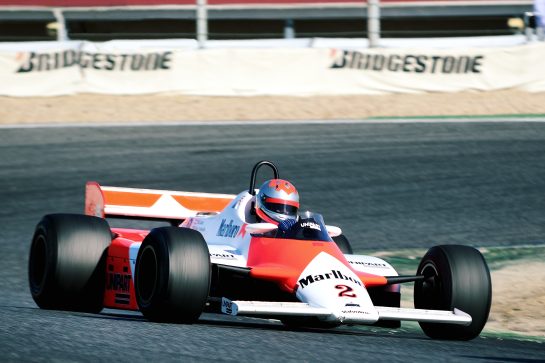
By the 1990s, production of even larger carbon composite pieces became possible, helping to reduce weight in the new Boeing airliner, the 777. The 777 was critical in introducing large composite pieces to aerospace, with the plane being 9% carbon composites by weight, being used in the rear fuselage, engine cowlings, control surfaces, and floor beams. In addition to saving weight, these new composite components were corrosion and fatigue resistant, which helped save on maintenance over the old industry-standard aluminum.
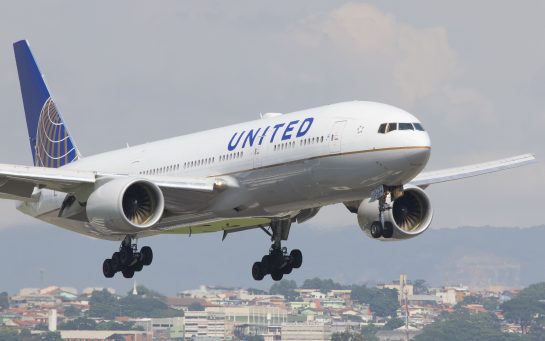
In 2007, Boeing introduced the revolutionary 787 Dreamliner which saw a massive increase the use of composites, now up to 50% by weight. Due to Boeing’s ability to produce large carbon composite pieces, the fuselage of the 787 is composed of three large single-laid sections that are then mated during assembly. Additionally, the wings of the 787 are primarily composed of carbon composites, with the materials ductility lending to the plane’s iconic wing flex.
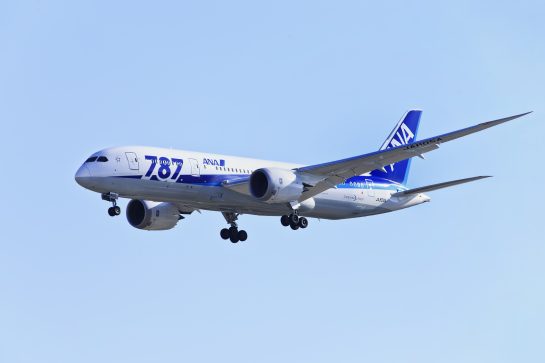
With these desirable characteristics in mind, it was only a matter of time before an application came up that required carbon composites. To minimize unit weight and maximize rotor inertia in the new TGD 129-114 generator unit, ThinGap’s new assembly uses carbon composite for both the inner and outer sleeves that retrain the rotor’s magnets and are joined together by a purposely designed metallic top cap with fan blades that forces airflow across the stator. To learn more about ThinGap’s custom and modified capabilities, click here.